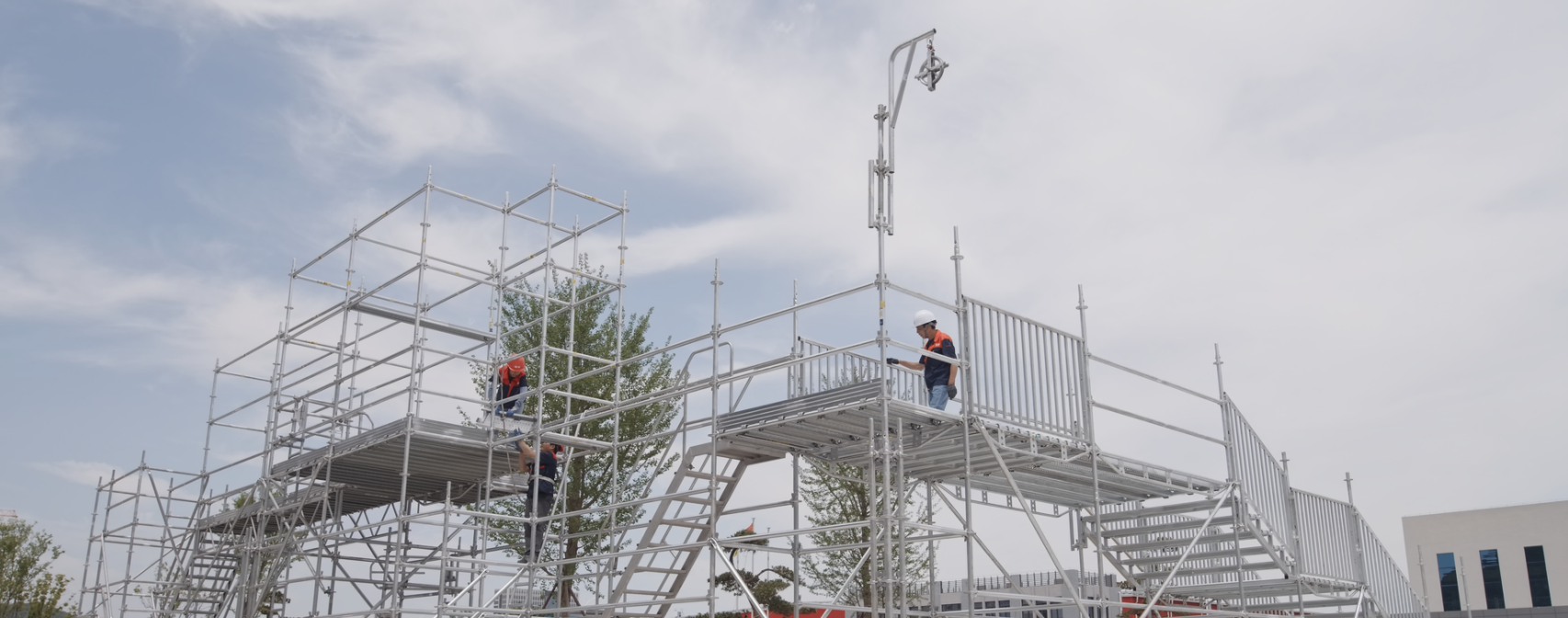
Why Dust Stops Work on Saudi Sites—And How Ringlock Scaffolding Solves It
Why Dust Stops Work on Saudi Sites—And How Ringlock Scaffolding Solves It
In Saudi Arabia's construction landscape, contractors are no strangers to delays. But one common culprit is often overlooked: dust.
From NEOM's wide-open desert sites to the industrial zones of Dammam, windborne sand and fine debris don't just affect visibility—they infiltrate equipment, damage joints, and disrupt progress. For scaffolding systems in particular, the impact is more severe than many realize.
The Real Cost of Dust in Scaffolding Operations
While dust may seem harmless compared to structural failures or high temperatures, its long-term impact on scaffolding systems is both technical and financial:
1.Joint Malfunction from Particle Buildup
In traditional systems, especially bolt-based or loose-fitting types, fine sand gets lodged in couplers, pinholes, and sleeves. This causes:
Difficulty in locking components
Misalignment during setup
Need for frequent cleaning or rework
When connectors don’t close properly or need hammering into place, your team wastes time and risks unsafe assemblies.
2. Accelerated Surface Wear and Internal Corrosion
Dust particles act like sandpaper, especially when trapped between metal contact points. Over time, this leads to:
Abrasion on mating surfaces
Coating breakdown and exposure to oxidation
Tightening issues or long-term loosening
What starts as a minor friction issue can evolve into a full system failure—right in the middle of a build.
3. On-Site Productivity Loss
Crews report that during sandstorms or heavy winds, the first thing to suffer is the scaffolding interface itself:
Brackets won't align
Pins won't insert fully
Assembly speed drops by 40–60% on dusty days
For time-sensitive Saudi projects, this means missed milestones, higher labor costs, and increased fatigue on site teams.
Why Ringlock Performs Differently in Dust-Heavy Conditions
While no system is completely immune to the elements, Ringlock scaffolding has several built-in advantages when it comes to sand and dust exposure—especially the system manufactured by HJ Scaffolding:
1.Gravity-Locked Rosette Connections
Unlike screw or wedge systems that rely on clean threads or narrow grooves, Ringlock uses a gravity-assisted wedge and rosette mechanism that self-locks—even with minor dust contamination.
2.Hot-Dip Galvanized for Dust Resistance
HJ Scaffolding's components are treated with a full hot-dip galvanization process, forming a thick zinc layer that resists abrasion and protects the steel even when sand wears on surfaces.
3.Precision-Fit System Manufactured In-House
With robotic welding, laser cutting, and ISO 9001 + EN 1090 certification, each Ringlock component is dimensionally consistent—meaning parts still fit even after field exposure, reducing on-site frustration.
What Smart Contractors in Saudi Arabia Are Doing Differently
Across major Saudi projects, especially those in dusty, undeveloped areas, contractors are:
Moving away from traditional pipe-and-coupler systems
Standardizing Ringlock to ensure fast installation and fewer delays
Choosing manufacturers that supply full systems, not just piecemeal parts
Dust won't go away. But with the right scaffolding system, its impact on your schedule and site safety can be minimized.
Ready to Upgrade Your Scaffolding?
At HJ Scaffolding, we manufacture and supply complete Ringlock systems designed to withstand the realities of the Middle East:
Hot-dip galvanized finish
Robotic welding & laser-cut components
Full system production—not just partial kits
Certified to ISO 9001, EN 1090, ISO 3834, and DASt 022 standards
If you're facing sand-related issues or tired of daily clean-up and fitting struggles—let's talk.
Web:www.hj-scaffolding.com
E-mail:lynn.li@hj-scaffolding.com
WhatsApp: +86 15058750031